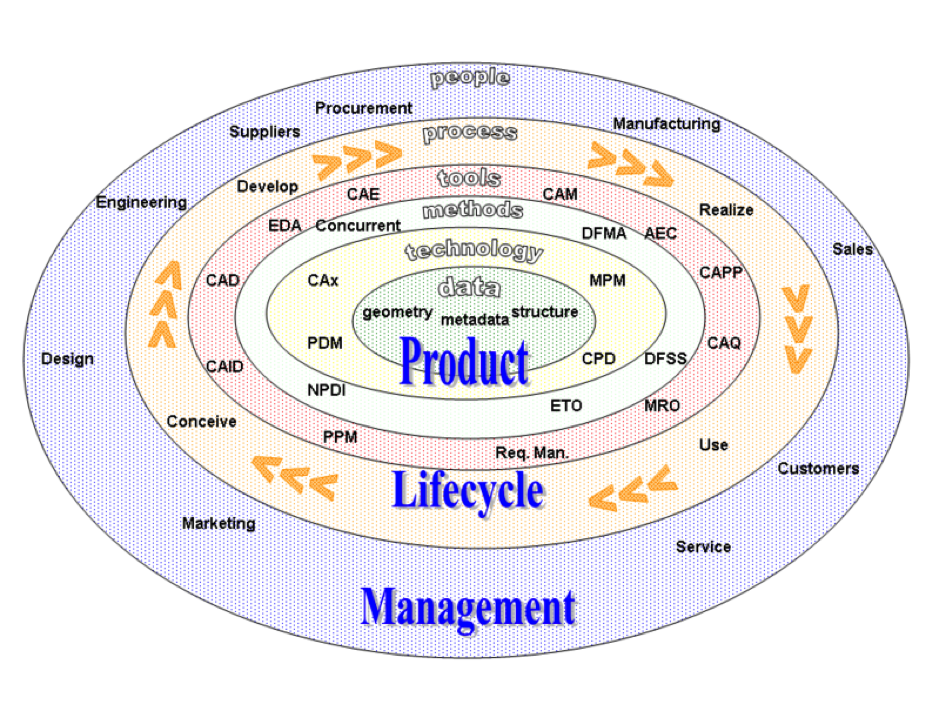
DATA
Geometry
Geometry is a branch of mathematics concerned with questions of shape, size, relative position of figures, and the properties of space.
Metadata
Metadata is “data about data”. The term is ambiguous, as it is used for two fundamentally different concepts (types). Structural metadata is about the design and specification ofdata structures and is more properly called “data about the containers of data”; descriptive metadata, on the other hand, is about individual instances of application data, the data content.
Structure
Structure is a fundamental, tangible or intangible notion referring to the recognition, observation, nature, and permanence of patterns and relationships of entities. This notion may itself be an object, such as a built structure, or an attribute, such as the structure of society. From a child’s verbal description of a snowflake, to the detailed scientific analysis of the properties of magnetic fields, the concept of structure is now often an essential foundation of nearly every mode of inquiry and discovery in science, philosophy, and art. The description of structure implicitly offers an account of what a system is made of: a configuration of items, a collection of inter-related components or services. A structure may be a hierarchy (a cascade of one-to-many relationships), a network featuring many-to-many links, or a lattice featuring connections between components that are neighbors in space.
TECHNOLOGY
Manufacturing Process Management (MPM)
Manufacturing Process Management (MPM) is a collection of technologies and methods used to define how products are to be manufactured.
MPM differs from ERP/MRP which is used to plan the ordering of materials and other resources, set manufacturing schedules, and compile cost data.
A cornerstone of MPM is the central repository for the integration of all these tools and activities aids in the exploration of alternative production line scenarios; making assembly lines more efficient with the aim of reduced lead time to product launch, shorter product times and reduced work in progress (WIP) inventories as well as allowing rapid response to product or product changes.
Product Data Management (PDM)
Product Data Management (PDM) is the business function often within product lifecycle management that is responsible for the management and publication of product data. In software engineering, this is known as version control.
Collaborative Product Development (CPD)
Collaborative Product Development (CPD) is a business strategy, work process and collection of software applications that facilitates different organizations to work together on the development of a product. It is also known as collaborative product definition management (cPDM)
Computer-aided Technologies (CAx)
Computer-aided Technologies (CAx) is a broad term that means the use of computer technology to aid in the design, analysis, and manufacture of products.
Advanced CAx tools merge many different aspects of the Product Life Cycle Management (PLM), including design, finite element analysis (FEA), manufacturing, production and product.
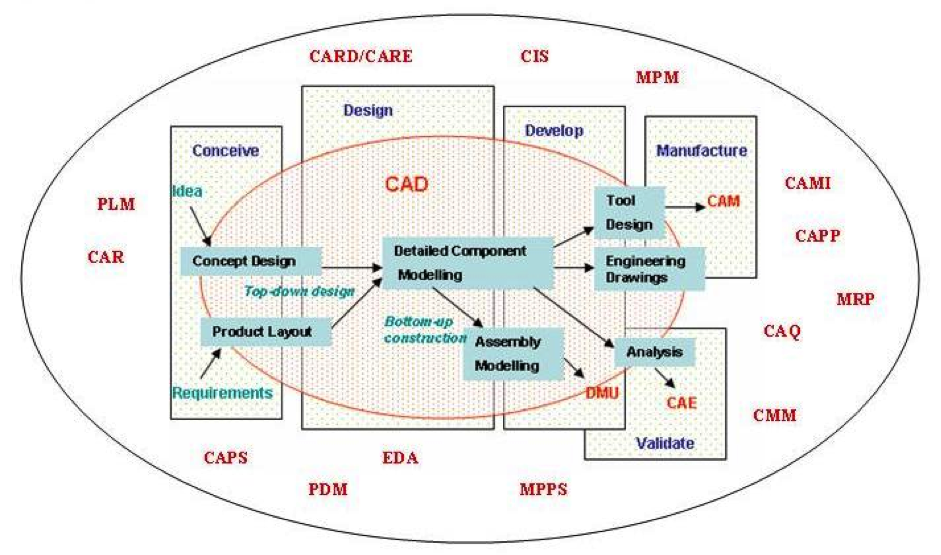
METHODS
Building Information Modeling (BIM)
Building Information Modeling (BIM) is a digital representation of physical and functional characteristics of a facility. A BIM is a shared knowledge resource for information about a facility forming a reliable basis for decisions during its life-cycle; defined as existing from earliest conception to demolition.
Traditional building design was largely reliant upon two-dimensional drawings (plans, elevations, sections, etc.). Building information modeling extends this beyond 3D, augmenting the three primary spatial dimensions (width, height and depth) with time as the fourth dimension (4D) and cost as the fifth (5D), etc. BIM therefore covers more than just geometry. It also covers spatial relationships, light analysis, geographic information, and quantities and properties of building components (for example, manufacturers’ details).
BIM involves representing a design as combinations of “objects” – vague and undefined, generic or product-specific, solid shapes or void-space oriented (like the shape of a room), that carry their geometry, relations and attributes. BIM design tools allow extraction of different views from a building model for drawing production and other uses. These different views are automatically consistent, being based on a single definition of each object instance. BIM software also defines objects parametrically; that is, the objects are defined as parameters and relations to other objects, so that if a related object is amended, dependent ones will automatically also change. Each model element can carry attributes for selecting and ordering them automatically, providing cost estimates as well as material tracking and ordering.
For the professionals involved in a project, BIM enables a virtual information model to be handed from the design team (architects, landscape architects, surveyors, civil, structural and building services engineers, etc.) to the main contractor and subcontractors and then on to the owner/operator; each professional adds discipline-specific data to the single shared model. This reduces information losses that traditionally occurred when a new team takes ‘ownership’ of the project, and provides more extensive information to owners of complex structures.
Use of BIM goes beyond the planning and design phase of the project, extending throughout the building life cycle, supporting processes including cost management, construction management, project management and facility operation.
Design for Manufacture and Assembly (DFMA)
Design for Manufacture and Assembly (DFMA) is the combination of two methodologies; Design for Manufacture, which means the design for ease of manufacture of the parts that will form a product, and Design for Assembly, which means the design of the product for ease of assembly.
Design for Six Sigma DFSS
Design for Six Sigma DFSS is a separate and emerging business-process management methodology related to traditional Six Sigma. While the tools and order used in Six Sigma require a process to be in place and functioning, DFSS has the objective of determining the needs of customers and the business, and driving those needs into the product solution so created. DFSS is relevant to the complex system/product synthesis phase, especially in the context of unprecedented system development. It is process generation in contrast with process improvement.
There are different options for the implementation of DFSS. Unlike Six Sigma, which is commonly driven via DMAIC (Define – Measure – Analyze – Improve – Control) projects, DFSS has spawned a number of stepwise processes, all in the style of the DMAIC procedure. Another option is, however, to integrate the DFSS approach into theProduct Development Process.
Engineer to Order (Built to Order) ETO
Engineer to Order (Built to Order) ETO sometimes referred to as make to order or made to order (MTO), is a production approach where products are not built until a confirmed order for products is received. BTO is the oldest style of order fulfillment and is the most appropriate approach used for highly customized or low volume products.
Concurrent Engineering (CE)
Concurrent Engineering (CE) is a work methodology based on the parallelization of tasks (i.e. performing tasks concurrently). It refers to an approach used in product development in which functions of design engineering, manufacturing engineering and other functions are integrated to reduce the elapsed time required to bring a new product to the market.
New Product Development and Introduction (NPDI)
New Product Development and Introduction (NPDI) improves alignment between a company’s product innovation process and its business strategy. The solution helps companies prioritize their innovation pipeline, providing a portfolio view of products and categorizing them based on various parameters such as market share, growth potential, and lifecycle stage. In addition, Daptiv for NPDI allows companies to take a project-based approach to new product introduction, providing pre-configured templates to manage scoping, business analysis, design and development, testing and validation, and product launch.
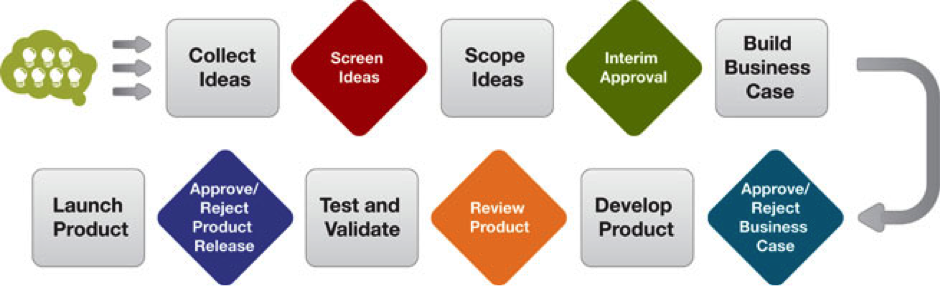
TOOLS
Computer Aided Design (CAD)
Computer Aided Design (CAD) is the use of computer systems to assist in the creation, modification, analysis, or optimization of a design. CAD software is used to increase the productivity of the designer, improve the quality of design, improve communications through documentation, and to create a database for manufacturing. CAD output is often in the form of electronic files for print, machining, or other manufacturing operations.
Computer Aided Process Planning (CAPP)
Computer Aided Process Planning (CAPP) is the use of computer technology to aid in the process planning of a part or product, in manufacturing. CAPP is the link between CAD and CAM in that it provides for the planning of the process to be used in producing a designed part.
Computer Aided Production Planning CAPP
Computer Aided Production Planning CAPP is used in different context on different parts of the production process; to some extent CAPP overlaps with the term “PIC” (Production and Inventory Control).
Process planning translates design information into the process steps and instructions to efficiently and effectively manufacture products. As the design process is supported by many computer-aided tools, computer-aided process planning (CAPP) has evolved to simplify and improve process planning and achieve more effective use of manufacturing resources. Process planning is of two types as;
- Generative type computer aided process planning.
- Variant type process planning.
Computer Aided Quality (CAQ)
Computer Aided Quality (CAQ) is the engineering application of computers and computer controlled machines for the definition and of the quality of products.
Maintenance Repair and Operations (MRO)
Maintenance Repair and Operations (MRO) involves fixing any sort of mechanical plumbing or electrical device should it become out of order or broken (known as repair, unscheduled, or casualty maintenance). It also includes performing routine actions which keep the device in working order (known as scheduled maintenance) or prevent trouble from arising (preventive maintenance). MRO may be defined as, “All actions which have the objective of retaining or restoring an item in or to a state in which it can perform its required function. The actions include the combination of all technical and corresponding administrative, managerial, and supervision actions.”
Requirements Management (RM)
Requirements Management (RM) is the process of documenting, analyzing, tracing, prioritizing and agreeing on requirements and then controlling change and communicating to relevant stakeholders. It is a continuous process throughout a project. A requirement is a capability to which a project outcome (product or service) should conform.
Project Portfolio Management (PPM)
Project Portfolio Management (PPM) is the centralized management of processes, methods, and technologies used by project managers and project management offices (PMOs) to analyze and collectively manage current or proposed projects based on numerous key characteristics. The objectives of PPM are to determine the optimal resource mix for delivery and to schedule activities to best achieve an organization’s operational and financial goals ― while honouring constraints imposed by customers, strategic objectives, or external real-world factors.
Product Portfolio Management (PPM)
Product Portfolio Management (PPM) – Product management is an organizational lifecycle function within a company dealing with the planning, forecasting, or marketing of a product or products at all stages of the product lifecycle.
Computer Aided Industrial Design (CAID)
Computer Aided Industrial Design (CAID) is a subset of computer-aided design (CAD) that includes software that directly helps in product development.
Within CAID programs designers have the freedom of creativity, but typically follow asimple design methodology:
- Creating sketches, using a stylus
- Generating curves directly from the sketch
- Generating surfaces directly from the curves
The end result is a 3D model that projects the main design intent the designer had in mind. The model can then be saved in STL format to send it to a rapid prototyping machine to create the real-life model. CAID helps the designer to focus on the technical part of thedesign methodology rather than taking care of sketching and modeling—then contributing to the selection of a better product proposal in less time. Later, when the requisites and parameters of the product have been defined by means of using CAID software, the designer can import the result of his work into a CAD program (typically a Solid Modeler) for adjustments prior to production and generation of blueprints and manufacturing processes.
What differentiates CAID from CAD is that the former is far more conceptual and less technical than the latter. Within a CAID program, the designer can express him/herself without extents, whilst in CAD software there is always the manufacturing factor.
Electronic Design Otomation (EDA)
Electronic Design Otomation (EDA or ECAD) is a category of software tools for designing electronic systems such as printed circuit boards and integrated circuits. The tools work together in a design flowthat chip designers use to design and analyze entire semiconductor chips.
Computer Aided Engineering (CAE)
Computer Aided Engineering (CAE) is the broad usage of computer software to aid in engineering analysis tasks. It includes Finite Element Analysis (FEA),Computational Fluid Dynamics (CFD), Multibody dynamics (MBD), and optimization.